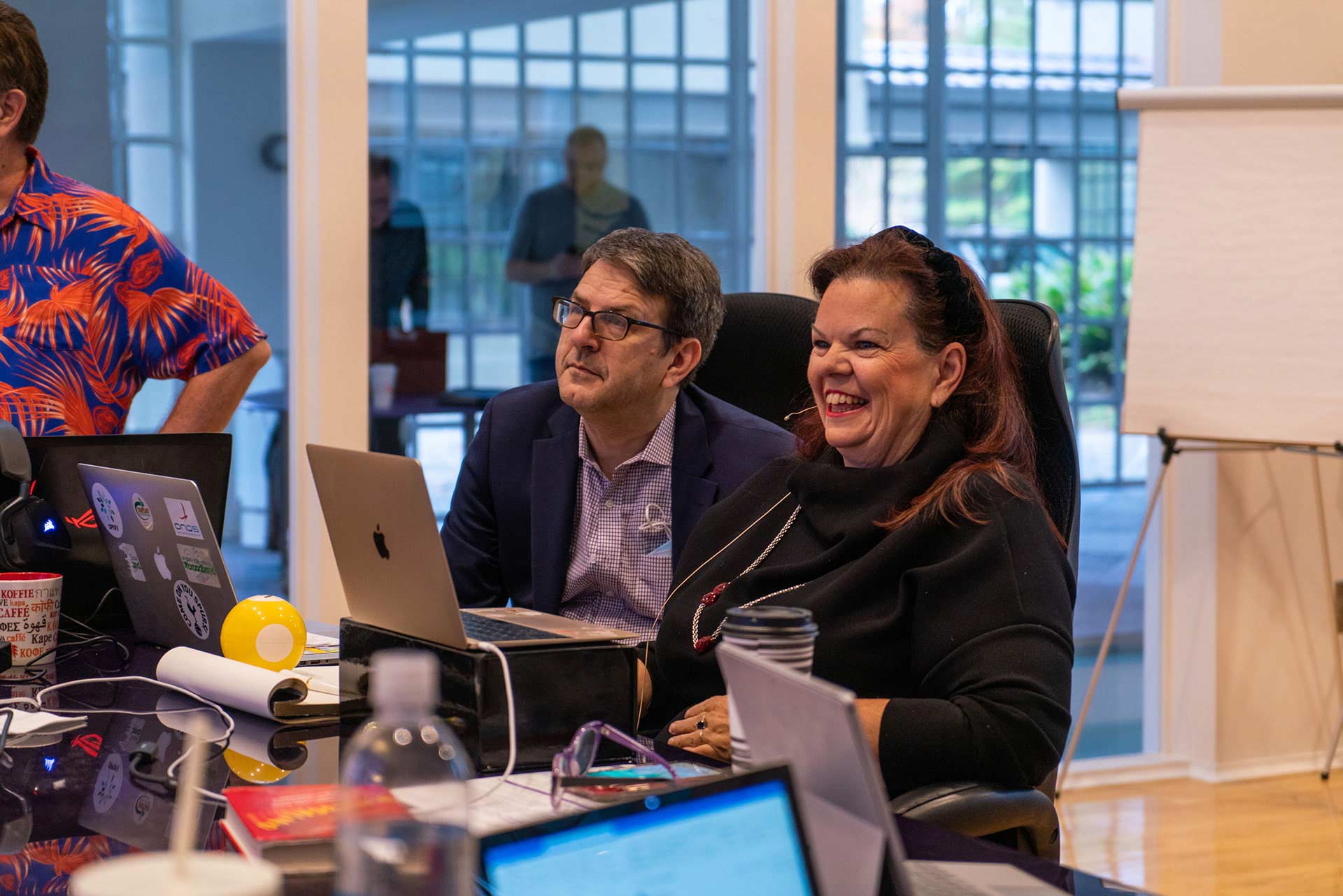
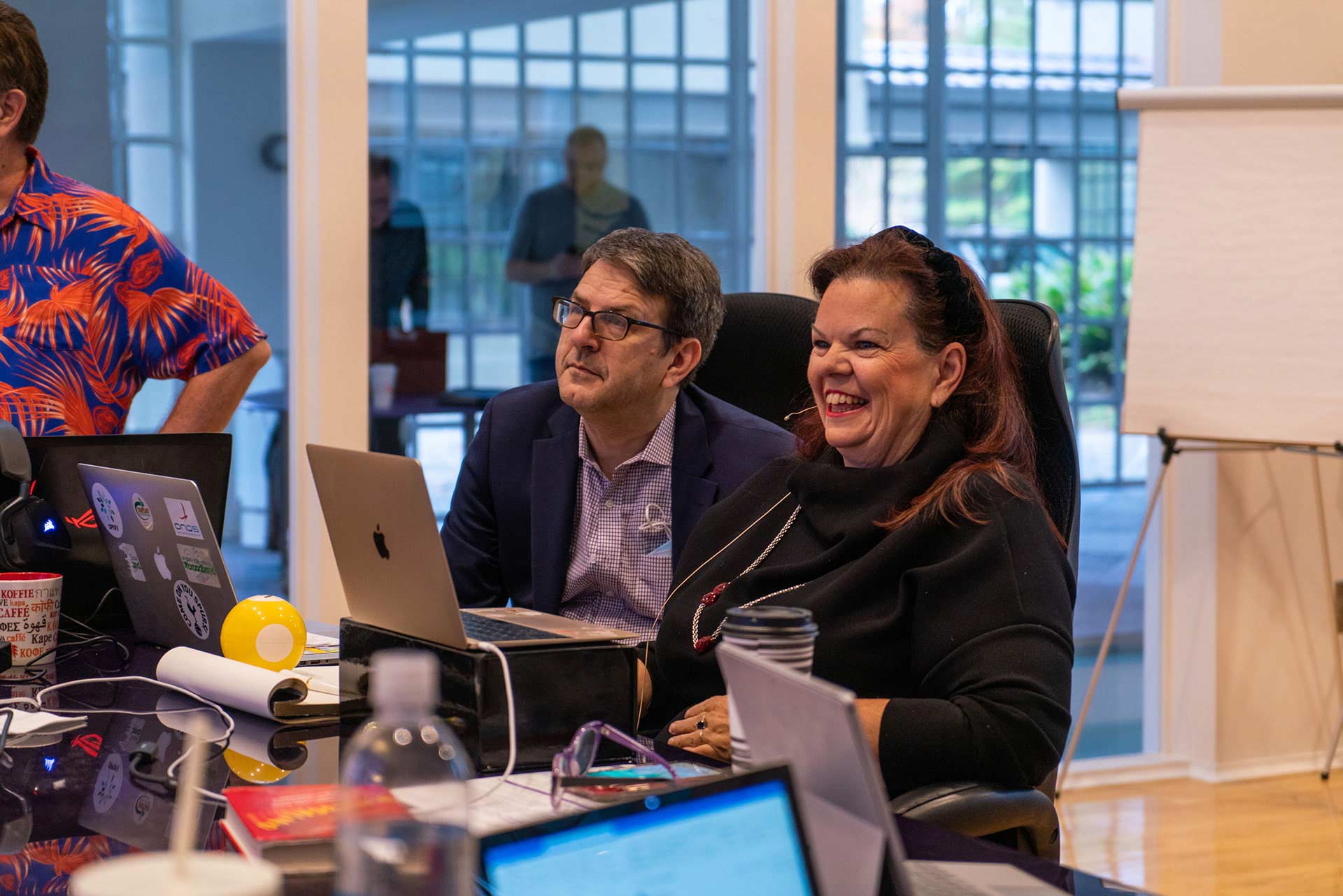
This article was featured in a February 2019 of American Pharmaceutical Review.
In general, what are some current issues facing pharmaceutical companies in regards to pharmaceutical technician/employee training?
Having led global quality organizations for many years, I had the opportunity to see first-hand the many challenges of ensuring that employees had the appropriate level of knowledge; and that their knowledge then translated to skills, motivation and commitment to do the right thing when faced with inevitable issues in pharmaceutical manufacturing and analysis. Unfortunately, over time, our industry has regressed from educating our employees on the technical and scientific implications of why we work in the manner we do, to very specific and limited transactional training associated with execution. A highly skilled employee requires both and deserves both: education and training. When people understand “the why” behind the requirements of a process, behavioral psychology data shows us that they are increasingly committed and motivated with a sense of responsibility in performing their functions correctly. In our industry, skill and motivation are both critical to a high performing organization and to the corporate bottom line.
Another challenge in today’s highly competitive market is to deliver efficient and impactful learning models that will provide the rapidly changing skillsets demanded by advances in emerging therapies and manufacturing technologies. At the same time, existing demands for standardization across global landscapes continue to pressure existing practices. Our industry’s outdated approach of focusing on transactional, procedure-based training only expands the need for investment in resources as unfortunately the industry has not kept pace with the ever increasing need and demand.
I would also say that we have all too often simply accepted the costs associated with deviations, recalls, batch rejections and other poor quality events, as simply a cost of doing business and that there is little that can be done on a human-factor level to move that needle. Other industries do not accept this predisposed position and neither should pharma. Continuous improvements, lead by a highly educated workforce, can and will reduce these costs, benefiting the company’s bottom line as well as benefiting the patient with a more consistent flow of safe medications. Continuous improvement only begins with continuous learning.
How can technology in general help pharmaceutical companies better train their employees?
Our world has significantly changed due to technology; we can see this everywhere in our personal lives. Frankly it is time for us to catch up in the life sciences sector and benefit from these advancements.
When Quality Executive Partners (QxP) began to look at pursuing the development of an educational platform with broad impact, we quickly recognized that technology was central to achieving this goal. People based educational solutions have lost the critical mass necessary to meet these needs at the demanded scale. Industry internal subject matter experts are already overloaded with the tasks of bringing new products and processes to market and resolving the issues of the day to maintain daily operations of their respective organizations. Computer-based learning can be effective and certainly plays a role, but again this often takes the highly valuable SME away from other critical tasks as a significant amount of time is needed to develop and maintain the content internally.
So, as we look across the industry today and talk with key leaders, we consistently hear that the industry is too reliant on, and has a false security in, the “read and understood” learning model. This approach is utilized far too often and rarely delivers consistent and comprehensive understanding, much less positively affecting skills and behaviors.
The key in advancing learning, which has a positive impact on patients and a profitable impact on the business, lies in providing on-demand high-quality technical material, which is engaging and fun, immediately relevant, and scalable across the entire corporate enterprise. This requires technology and expertise in both content and the technologies deployed.
Virtual Reality (VR) has been making in-roads into many industries. How is it applied to the pharmaceutical industry? Are there specific challenges to making VR work and be applicable to the industry?
Virtual Reality is a term that is getting a lot of play in the life sciences sector, and there is a very broad understanding, and often times a misunderstanding, of the various types of VR and their intended application. We regularly see that companies are interested in innovation projects associated with VR, almost seemingly to be able to say that they employ VR technology without a clear understanding of how the technology can, and should, be applied to improve their businesses. The two most often utilized technologies in pharma are the “see what I see” applications, which is really not VR, and VR simulators, which are not interactive or immersive. Both could have application, but are very limited when compared with fully interactive and immersive Virtual Reality.
The two biggest challenges to making VR work for an organization, and moreover ensuring that it has a positive impact, lies in the level and application of the technology utilized, and the capability and pharmaceutical technical knowledge of the development team. Interactive and immersive VR is the highest level of VR capability and offers the greatest benefit in building skills and retention.
The most critical factor in VR development, as in most revolutionary innovations, is the development team. Our Virtuosi team of pharma technical experts and our VR developers are first and foremost engineers and scientists who understand the critical learning objectives of pharmaceutical processes, as well as what mistakes are commonly made in manufacturing and laboratory environments. Our highly skilled VR engineers build upon this foundation to develop realistic graphics, interactions, and feedback loops that allow learners to practice their skills in a fully interactive environment that provides real-time coaching and consistent performance feedback. This combination of skills and industry expertise has allowed us to develop a truly unique educational product that is the only comprehensive product of its kind available anywhere in the world.
Can you describe the Virtuosi platform and its features and benefits? How is the Virtuosi approach to pharmaceutical learning/training different than other training systems?
Virtuosi is a fully integrated educational platform leveraging the power of interactive, immersive VR. Our first educational series focuses on Sterile Product Manufacturing and Microbiology. It has been thoughtfully designed with clear learning objectives based upon our expansive view of the topics and understanding of the critical learning parameters necessary to develop deep understanding, practical skill and confidence in performance.
This series consists of over 80 hours of education and skill development broken down into 31 educational modules covering all aspects of sterile product manufacturing and microbiology laboratory operations. Modules are organized into comprehensive curricula, which are customizable to the needs of the learner and progressive in technical difficulty to build knowledge and skill over time. Within these modules are 16 interactive, immersive VR experiences where the learner can apply their knowledge, experience success, and build skills to defined proficiency levels.
As an on-demand solution, learners progress at their own pace with the ability to repeat topics and experiences or to use as a reference for situations such as deviation investigations.
The most unique aspect of the Virtuosi experience is that it provides a safe space where mistakes can be made, removing potential for embarrassment and fear of being wrong, as well as individual and private real-time virtual coaching, which is unique to their actions within the virtual environment. Experiencing failure engages learning, which further embeds comprehensive understanding of “the why”.
Studies have shown that interactive, immersive VR substantially improves learning and knowledge recall as these interactions and experiences leverage the brain’s pre-wired capability to encode and store spatial and visual inputs more efficiently. This is a key differentiator from any other learning system, approach or application available today.
Specifically, can you detail the benefits a pharmaceutical company might realize by employing this platform?
Virtuosi is a business solution. Driving top and bottom line growth is the objective of the platform and Virtuosi was designed specifically for these purposes.
Specific benefits of employing Virtuosi are vast based upon the objective of the company and deployment methodology. These opportunities include:
- Reduction of human error leading to batch rejections and deviations; reducing direct costs for lost time and materials, indirect costs in the labor necessary to investigate and correct them, as well as equipment down time and lost production opportunity;
- Support of organizational scale-up and growth where time to competency is critical;
- Promotes education as desirable, fun and important;
- Creates a personalized on-demand learning environment that allows the learner to take control of his/her own growth and development;
- Limits and protects the operational environment allowing for reduced equipment usage for training and risks of environmental contamination; and
- Standardizes expectations across an enterprise and allows for self-inspection of operational practices aiding in continuous improvement.
Looking ahead, how will QxP continue to offer its current and future customers the best available platforms and training materials?
It has taken an extraordinary effort of 25 very talented and driven professionals over two years to deliver Virtuosi, and we are committed to maintaining the content and technology as these evolve. Quality Executive Partners participates in many forums as thought leaders and influencers on technical and regulatory content, as well as VR technologies. As regulations and industry practices evolve, our product managers will constantly review our content and technology leading to updates so that our clients have the latest education in procedures and techniques. We are deeply entrenched in the VR technology community and are constantly evaluating new components and technologies prior to their release into the mainstream. Additionally, we will host User Communities with different areas of focus to gain insights and recommendations for content changes and continuous improvement. Further series are under development, including biotechnology, solid dose manufacturing and chemistry laboratory operations.
‍