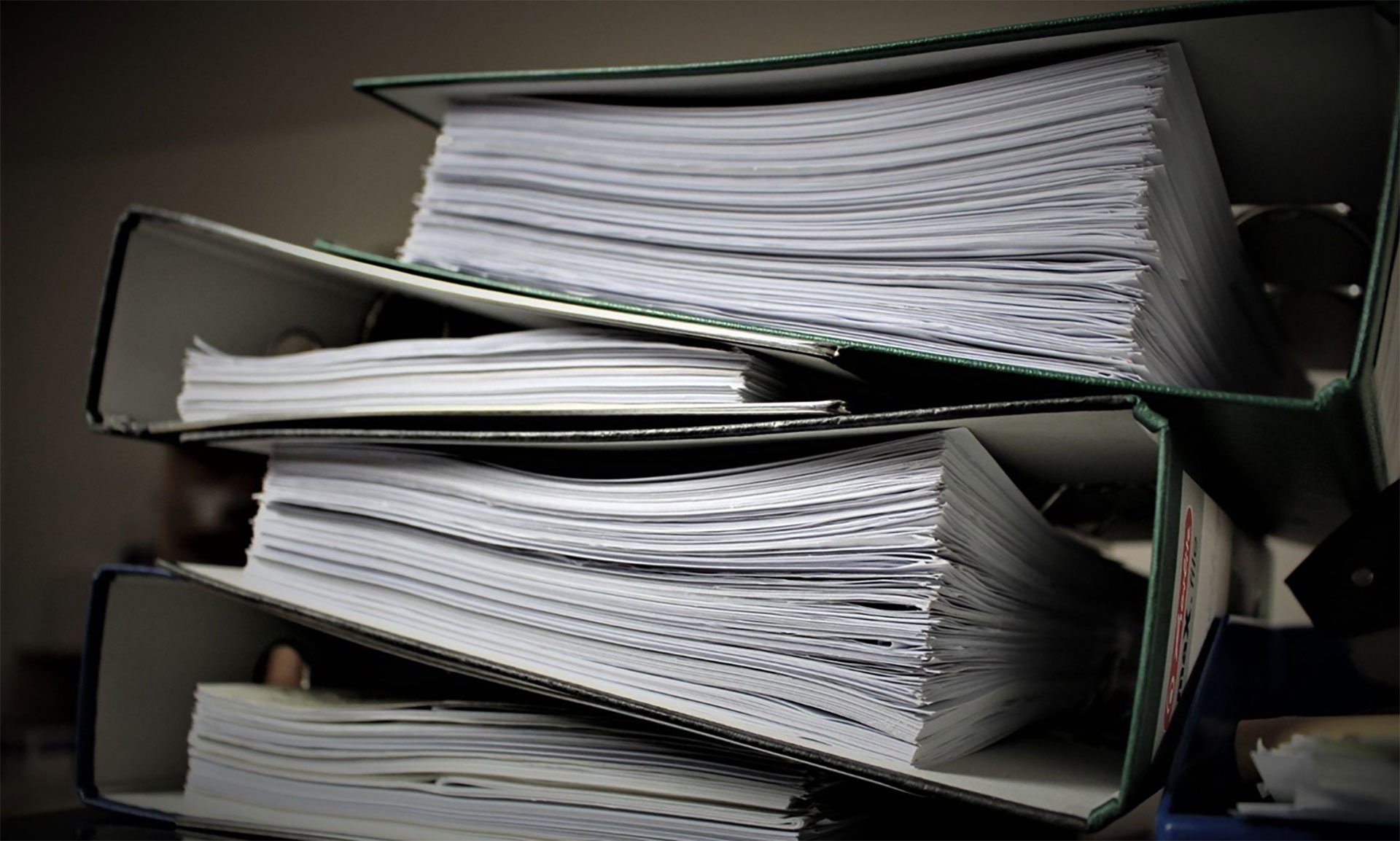
The Key to Reducing Deviations, Delays, and Product Loss in Pharmaceutical Manufacturing
“Kids are like sponges!” This is a comment we have all heard about how quickly kids pick up and internalize learning. Words, concepts, and language all seem to be easily absorbed and retained by children of all ages. Then we grow up and suddenly just remembering where the car keys are located becomes a challenge.
I had intended to quote several neuroscientists about the differences between kids and adults, but if you are over 25 and have attempted to learn a new skill or language, you understand the challenges of adult learning. Becoming proficient at something new requires focus, repetitive practice, and sufficient time to absorb and retain the details. Not rocket science, but we in the pharmaceutical and biopharmaceutical industries apparently think the people who work for us are different. We cram training into short segments or only when production schedules allow. We ask our people to ‘read and understand’ procedures which sometimes exceed 30 pages in length. Then we give them a chance to observe a trained technician, perform the skill a few times under supervision, and then become responsible for activities that are critical to the quality of the drugs they are manufacturing.
Despite these approaches, which any educator or trainer will confirm are minimally effective, senior management is surprised when errors occur that result in deviations, delays or, all too often, product rejection. To further compound the problem, the resulting investigation and corrective action often focuses on “retraining” the technician.
In recent blogs and a fine article in the European Journal of Parenteral and Pharmaceutical Sciences, my colleague Tyler DeWitt has discussed the value of utilizing virtual reality as a training tool coupled with video lectures that allow the student to learn the fundamentals at their own pace, review critical knowledge as frequently as needed to internalize the information, and then practice in a safe environment the physical manipulations required.
In addition to incorporating state-of-the-art education tools and methods, we need to create an environment in our operations that recognizes how adults learn and how they maintain proficiency over time. Successful, consistent, and sustainable production requires well-trained and educated technicians, supervisors, and quality partners. Achieving this level of performance requires that several key elements be incorporated into the manufacturing culture.
-Training and education are not a supplemental activity. For new skills, the individual must be given sufficient time to learn, practice, and then demonstrate the skill. For experienced personnel, regular refresher sessions are essential.
-Curricula must be focused and targeted to the task. With today’s learning and education tracking software, it is too easy to dump courses and tasks into an individual’s requirements without regard to the benefit it provides in doing the role successfully.
-Roles and responsibilities must be clearly defined to keep skill development focused and effective. Often in the name of flexibility, we train our personnel to perform multiple tasks and the result is poor execution due to insufficient practice or too many tasks to master successfully.
-Knowledge Management is a key role in pharmaceutical and biopharmaceutical manufacturing operations. A person or group must bet asked with ensuring that the production team is trained and educated to perform optimally. This requires monitoring performance and performing continuous improvement on the curricula, methods, and material utilized for skill development and sustainability. It is not the administrative function of maintaining training records.
If we look outside our industry, there are numerous examples of critical jobs (e.g., airline pilots)or even sports teams that understand and apply these principles to develop and maintain optimal performance. We all understand in our industry that our patients rely on us to provide them with effective, high-quality pharmaceuticals. Recent news reports, such as “Drug Shortages Near All-Time High, Leading to Rationing”(1) demonstrate that we are not meeting that challenge. Changing our approach to training and education can be an important part of resolving this problem.
(1) Drug Shortages Near All-Time High, Leading to Rationing by Christina Jewett, New York Times, May 18, 2023
QxP Vice President Mike Levitt started his more than 30-year career in pharma leadership as Director of Production Operations at Eli Lilly and Company back in 1989.
Check out Mike’s other recent blog, “Six Keys for Effective Deviation Investigators.”